Image © CorkSol UK Ltd
Needing to improve the energy efficiency of their property, a York based family recently opted to use SprayCork on the exterior of their house.
The 1930s semi-detached property was constructed with solid brick, with insufficient render to the front and side. The rear extension was also covered in cracked and discoloured monocouche render, further contributing to the heat loss.
Following a comprehensive assessment, the property’s Energy Performance Certificate (EPC) displayed a score of D (60), indicating a relatively low energy efficiency level. However, the EPC also suggested that the property could achieve the potential C rating (79) by addressing the walls of the property as they did not hold a cavity.
Testing carried out by Aico identified that there was a high heat loss risk within the property. It also highlighted the average Time to Lose 1 degree (TTL) of 28 minutes, indicating a quicker rate of heat loss. The TTL value can be used to provide a comparison of heat loss across different homes, and is calculated by utilising both internal and external temperature conditions which provides an understanding about how quickly a room is losing heat to the outside world.
The solution
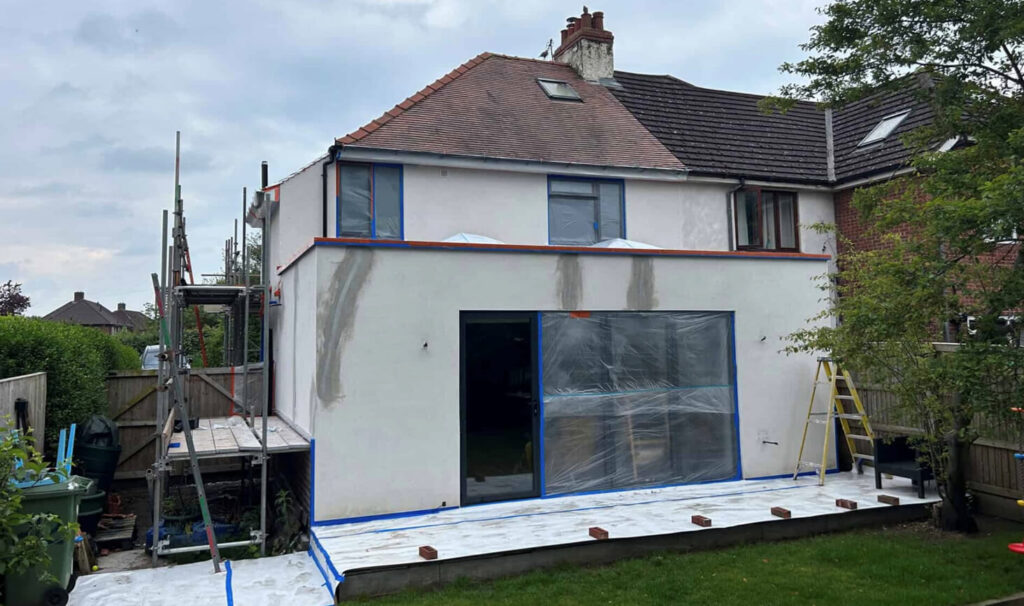
Image © CorkSol UK Ltd
Considering the lack of wall insulation, improving the fabric of the building would increase its energy efficiency. The property’s design presented specific challenges, as the first metre from the ground was exposed brick before stepping in slightly and becoming rendered. Although an external wall insulation system of 100mm – 150mm could cover this it wasn’t considered desirable. Furthermore, all the windows of the property would need to be removed and reinstalled. Independent CorkSol Applicator, JMB Plastering Specialists proposed using SprayCork to improve insulation, reducing the need for removal of existing fittings, and enhancing the property’s appearance. As the existing monocouche substrate was sound, SprayCork was simply applied as an overspray. For other areas, the process involved removing existing render, sealing and priming the brickwork ready for spraying.
The result
After monitoring the property for two months following the SprayCork application to evaluate the effectiveness of the solution, the results were then compared to the data taken before the application, using the HomeLINK dashboard.
The results showed a significant improvement in the property’s energy performance. Heat loss risk had changed from high across all three rooms to medium in 2 and low in 1. In line with this, the TTL 1 degree had increased from 28 minutes to 53 minutes – a huge increase of 25 minutes.
This demonstrated a huge improvement in the energy efficiency of the home.
To find out more about this case study: Download Case Study.
Another project where heating costs were reduced by 24%
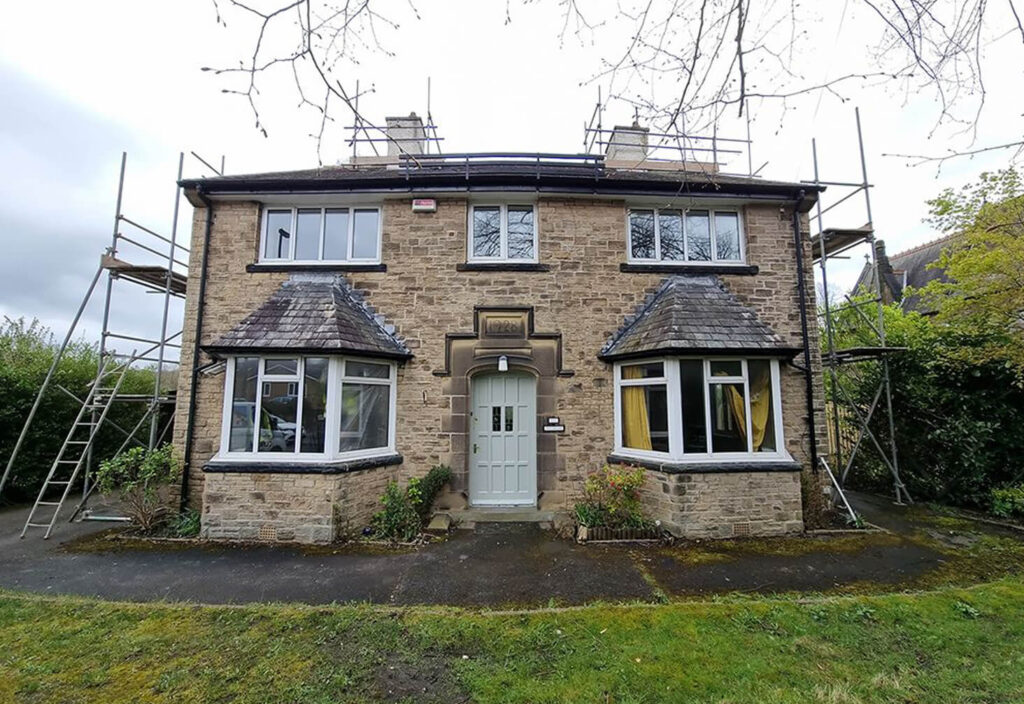
Image © CorkSol UK Ltd
The Diocese of Sheffield recently invited CorkSol to improve the energy efficiency of one of their vicarages that suffered from heat loss and high utility bills.
Mortomley Vicarage, a building with a unique stone front elevation and rough-cast-covered sides and rear walls, needed a sensitive approach to insulation that preserved its historic features.
The solution proposed by CorkSol involved applying SprayCork externally on the rear and side elevations and internally on the exterior walls, complemented by an overskim of breathable plaster. This method was chosen to boost energy efficiency without the need for invasive removal of existing wall substrates.
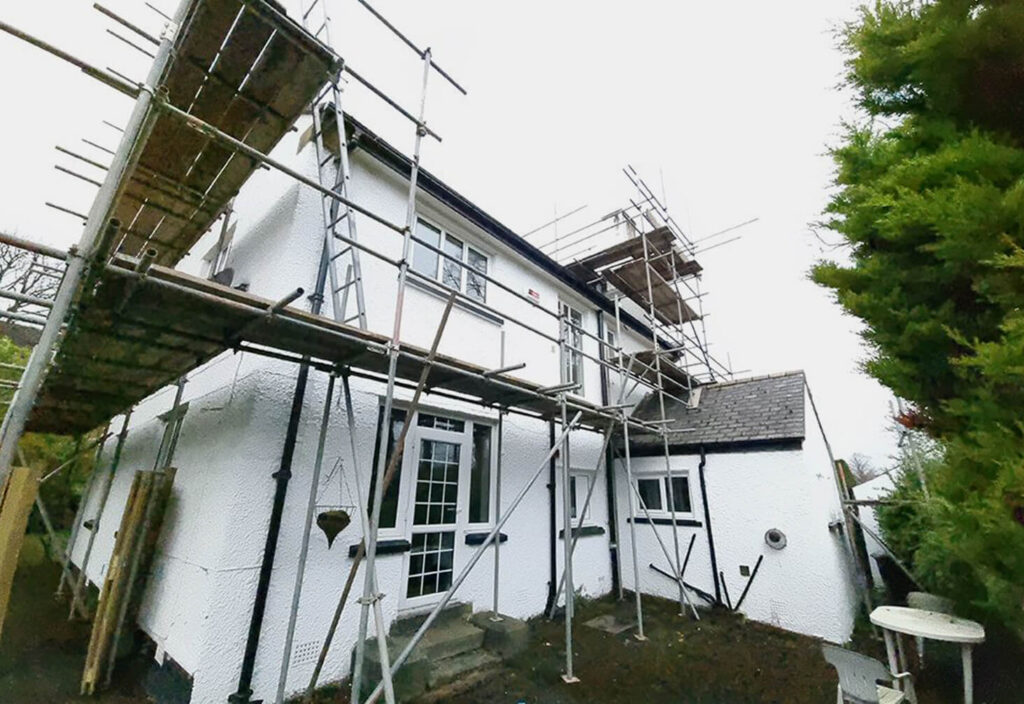
Image © CorkSol UK Ltd
To validate this approach, CorkSol enlisted the help of Build Test Solutions Ltd to conduct a thorough testing and evaluation. These tests included air permeability and U-value measurements taken before and after the SprayCork application. Conducted in March and June 2024, the tests measured the effectiveness of the insulation treatment over time.

Image © CorkSol UK Ltd
The results
The air permeability tests showed a significant reduction in unintended air leakage, indicating better insulation. Most notably, the U-value, which measures the rate of heat loss, improved by 24% in the ground floor front room. This improvement was in line with expectations based on SprayCork’s thermal properties and demonstrating its effectiveness in real-world applications.
But this isn’t the full story…
Unlike most insulation materials, cork does not require lots of energy to produce or create any ecological damage from mining or other processing. Taken from the bark of the cork oak without felling the tree or affecting wildlife habitats, cork re-grows naturally absorbing more CO2 from the atmosphere in the process than if it was left un-harvested.
It is rare to be able to take something from the Earth and have a positive effect on the environment.
For more information on this project or to discuss your requirements, contact James Erskine, Specification Sales Manager at CorkSol: james@corksoluk.com.
#CorkInsulation #CorkSol #SprayCork #ChurchOfEngland #Sheffield